Did not you find what you were looking for? Ask us! We have archives of 140 TB. We have all modern reuse projects and renovation projects for Soviet standard buildings. Write to us: info@proekt.sx
Boiler project 700 kW
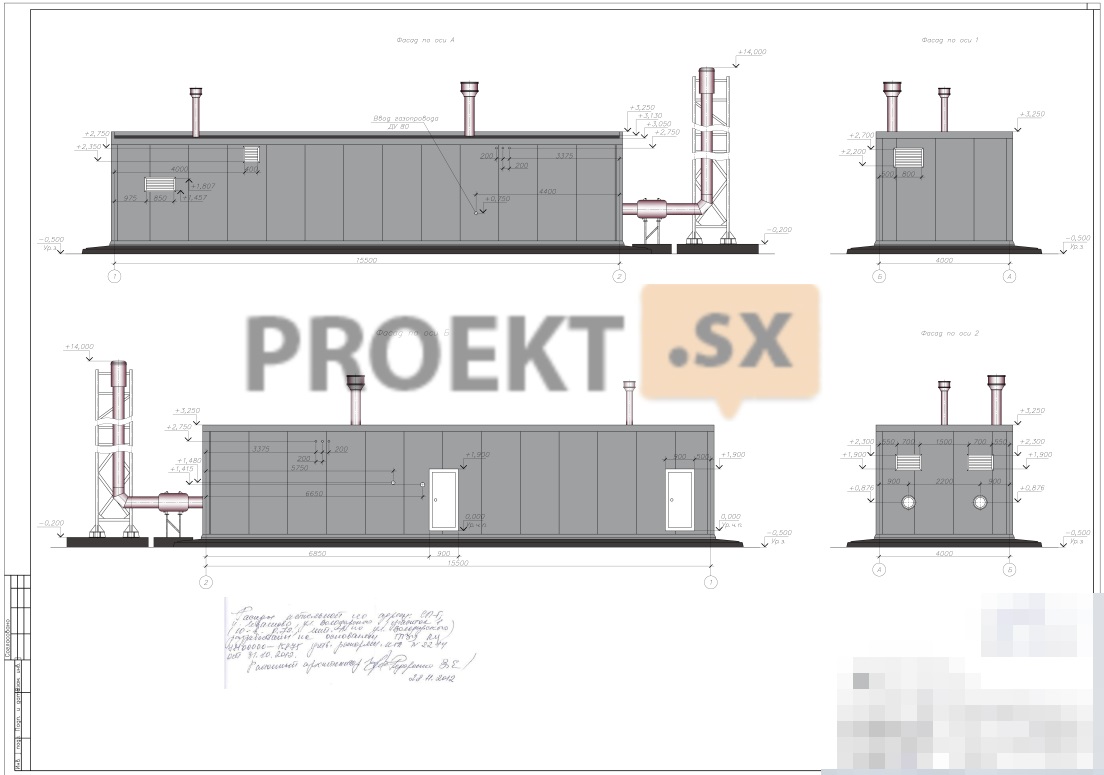
Design, working documentation, including estimates, and the results of engineering surveys for the construction of a block-modular gas boiler house with external engineering networks for heat supply to multi-apartment residential buildings
Technical and economic characteristics of the capital construction object
Plot area within the boundaries of the land allotment according to the town-planning plan, ha: 0,025
Building area, m2: 70,84
including:
Buildings, m2: 65,93
Foundation for the pipe, m2: 4,91
Total area, m2: 65,93
Construction volume, m3: 209,73
Floors, floor: 1
Productivity, kW: 700
The length of engineering networks, including: -
heating networks, r.m.: 121,1
water supply networks, lm: 70,0
sewerage networks, lm: 46,0
power supply networks, lm: 61,04
gas supply networks, lm: 50,2
Estimated cost at the 2001 base price level (without VAT)
Total, thousand rubles: 4781,75
Construction and installation works, thousand rubles: 1204,55
Equipment, thousand rubles: 2674,81
Other expenses, thousand rubles: 902,39
including:
PIR, thousand rubles: 519,80
refundable amounts, thousand rubles: 3,21
Estimated cost at current price level November 2012 (VAT included)
Total, thousand rubles: 22512,71
Construction and installation works, thousand rubles: 7142,08
Equipment, thousand rubles: 10446,58
Other expenses, thousand rubles: 4924,05
including:
PIR, thousand rubles: 2389,45
VAT, thousand rubles: 3393,13
refundable amounts, thousand rubles: 16,14
Structural and space-planning solutions
The modular boiler house is designed from easily assembled metal structures with "sandwich" paneling. Metal structures are made of a closed bent profile 100x4, 80x4, etc. (connections from a bent profile 80x4) according to GOST 30245-2003, the base of the module is made of I-beams 20B1 according to STO ASChM 20-93. Steel structures C245. The outer walls are hinged "sandwich" panels 100 mm thick. The coating is made of "sandwich" panels 100 mm thick on a metal frame. Spatial rigidity and stability of buildings is provided by vertical and horizontal connections. The foundations are taken in the form of a monolithic reinforced concrete slab 200 mm thick, concrete B15, W4, F75. Under the foundation, concrete preparation is provided with a thickness of 100 mm on a sand cushion of 350 mm. The chimney (2 flues) 14 m high and 350 mm in outer diameter are fixed on a spatial metal structure installed on its own foundation. The metal structures of the chimneys are made of racks (pipe with a diameter of 70x4) united by a grid of 60x40x4 bent-welded pipes. The foundations for the pipe are columnar from monolithic reinforced concrete. Concrete B25, W4, F75. The relative elevation of 0.00 corresponds to the absolute elevation of +15,75 m. In accordance with the report on engineering and geological surveys, the base of the foundations is dusty dense sand with E=270 kg/cm, cf=34°, c=0,06 kg/cm. The design resistance of the base soils is not lower than R=4,16 kg/cm. The pressure on the ground does not exceed p=0,67 kg/cm. The maximum level of groundwater is at a depth of 0,0-5 m. Groundwater is non-aggressive to concrete of normal permeability. In order to protect the concrete of underground structures, the surface of the concrete is protected by coating with MBR-65 mastic. The expected average settlement of the building is not more than 1,5 mm. Pipe stability is guaranteed.
Engineering equipment, utility networks, engineering activities
For the heat supply of heat consumption systems of residential buildings, it is planned to build a separate heating gas boiler house with an installed capacity of 700 kW. The boiler room is equipped with two hot water boilers Termotekhnik TT50 with a nominal heat output of 350 kW each, with Oilon burners: one with a GP-26.21H burner, the second with a GKP-26.21H burner. Estimated productivity of the boiler house - 337,0374 kW, including: for heating - 324,4770 kW; for losses in heat networks - 12,5604 kW. Fuel - natural gas with heat of combustion - 7980 kcal/m. The scheme for connecting heat networks for transporting the coolant to heat consumption systems is independent through plate heat exchangers. The water temperature at the outlet of the boilers is 105°C, at the outlet of the boiler room - 95°C. The design solutions provide for installation in the boiler room: two plate heat exchangers M6-FG with a heat output of 690 kW; circulation pumps for the boiler circuit IL65/160, two network pumps IPL40/120; expansion tanks of the boiler circuit with a volume of 100 liters; pumps MHI 205; expansion tank of the network circuit with a volume of 1000 l; expansion tank with a volume of 16 liters; hydraulic distributing device with a diameter of 219 mm. A chemical water treatment plant is provided based on the water treatment plant with Tecla APG 603 reagents. Commercial metering of thermal energy is provided. The temperature of the combustion products at the outlet of the boilers is 180°C. For the removal of combustion products, individual gas ducts and chimneys 14 meters high are provided. Design solutions provide for thermal insulation of equipment and gas ducts. Design solutions provide installation of a 16 kW SDMO Nexys Silent diesel generating set in a separate boiler room. The designed fuel tank with a volume of 0,8 m3, fuel lines and fittings provide for the possibility of operating the boiler house on liquid fuel when the gas supply is interrupted for the time of draining the heat consumption systems of buildings. The design solutions provide for the laying of heating network pipelines from the boiler house to the houses. Connection point - pipelines in the pit of the boiler room. The heating network is two-pipe. The heat carrier is water with parameters: Р1=43,82 m w.st.; Р2= 38,73 m w.st.; Т1/Т2=95/70°С. Thermal load of the heating system of house No. 72 - 0,1396 Gcal/h; house number 74 - 0,1396 Gcal / h. The laying of pipelines of the heating network is provided underground, channelless, at the corners of rotation - in monolithic channels and in cases under the driveways, as well as aboveground along the basements of buildings on low supports. For laying pipelines of the heat network, pipelines made of Casaflex corrosion-resistant steel in polyurethane foam insulation in a corrugated polyethylene sheath according to TU4937-023-40270293-2004 were selected, with above-ground laying in insulation with mineral wool cylinders with a cover layer of fiberglass and impregnation with liquid glass, when laying in a pit at house number 74 - with PPU spraying. Compensation for temperature elongation of pipelines is provided due to their self-compensation. Gas supply is provided in accordance with the Technical Specifications. The connection point is a medium-pressure polyethylene gas pipeline with a diameter of 63 mm, laid between residential buildings No. 72 and No. 74. The gas pressure at the connection point is 0,15 MPa. Natural gas consumption - 81,8 m3/h. From the connection point to the exit from the ground at the facade of the designed boiler house, alaying of an underground polyethylene PE100 GAS SDR11 gas pipeline of medium pressure with a diameter of 63 mm, further along the facade of the boiler room to the entry into the boiler room - a steel above-ground gas pipeline of medium pressure with a diameter of 57 cm. The gas pressure at the inlet to the boiler room is 219 MPa. Steel electric-welded longitudinal pipes according to GOST 0,15-10704, V-91 GOST 10-10705* were selected for laying. For commercial accounting of the amount of gas, a gas meter of the RVG G80 type is installed. At the entrance of the gas pipeline to the boiler room, the following are installed in series: gas filter FN25-2; thermostop valve KT2-3001, solenoid valve VN50N. Unit-wise gas metering is designed by RVG G2 meters. Water supply (cold water) and water disposal of the consumers of the facility is provided in accordance with the specifications. Water supply (cold water) is provided from public water supply networks D=250 mm through one inlet from pipes n3100SDR17 D=63 mm. The connection point is on the public water supply networks. At the input, a water metering unit is provided according to TsIRV 02A.00.00.00 (sheets 20, 21). Guaranteed pressure at the connection point -18m of water. Art. Estimated consumption of cold water - 1,55 m / day (feeding of heating networks, regeneration of filters, preparation of hot water, cleaning). The estimated consumption of cold water for periodic needs is 11,4 m / day (filling the heating network system and the boiler circuit once a year). Water consumption for internal fire extinguishing - 5,0 l / s (2 jets of 2,5 l / s). The building has an integrated plumbing system. The integrated water supply system is a dead-end, single-zone. The number of fire hydrants D=50 mm - 2 pcs. The required pressure for the integrated water supply system is 16,74 m of water. For the device of the integrated water supply system, steel water and gas pipes were selected. External fire extinguishing is provided from fire hydrants installed on public water supply networks. Water consumption for external fire extinguishing - 10 l / s. Removal of domestic wastewater in the volume - 0,02 m / day, periodic discharge - 11,4 m / day 1 time per year (emptying the system 1 time per year) is provided for the combined sewerage network D-250 mm taken out from under the building spots. Removal of rainwater with a flow rate of 1,17 l / s is provided for in the network of existing storm water wells on the network of the existing combined sewerage. Polypropylene two-layer corrugated sewer pipes D = 250 mm were selected for laying a network of combined sewerage. The following systems have been designed for the building: domestic sewerage (for the removal of conditionally clean effluents from process equipment), external drains. Cast-iron sewer pipes were chosen for the construction of domestic sewage systems. Power supply of a free-standing gas boiler house in a free area, in normal mode, is provided from public electric networks, according to the specifications, annex to the contract. Estimated power 17,9 kVA, voltage class 0,4 kV, connection points - the nearest support of VL 0,4 on the street, SIP wire, cross section 70 mm2. In emergency mode, when the ASU suddenly disconnects from the centralized power supply system, the power switches to an autonomous source - an engine - a 22 kVA generator set, which is switched on automatically. The category of power receivers in terms of power supply reliability is the second, therefore it is provided from two independent mutually redundant sources, power receivers of security systems, in addition (of the first category), are backed up from the UPS. The grounding device of the boiler house consists of a common artificial external ground and a natural ground electrode - the foundations and floor of the boiler house building and the foundation of the chimney. Electricity metering devices are installed on the ASU panels of the boiler room. The device of distribution and group networks - according to the standards, protective devices are installed on the panels of the ASU and local shields, lighting control devices and sockets for portable electrical receivers - on the walls. Grounding of open conductive parts of electrical equipment - through PE conductors in cables of the group and distribution network, the type of grounding system for open conductive parts - TN-S (separate), the equalization system and potential equalization comply with the standards. The adopted circuit design solutions of the electrical installation being designed ensure the electrical safety of uncategorized and operational personnel (solid insulation, shutdown of non-stationary processes, absence of contact voltage, etc.). Lightning protection of the building is provided lightning rods on chimneys, a metal frame of a boiler room with down conductor devices connected to the ground electrode.To organize a communication channel and data transfer to the CDL, it is planned to install a Cisco 800/1900 series border router, as well as equipment for organizing a channel - a 3G modem of the UMTS / SDMA standard (with a RUIM operator card "Sky Link"). For the installation of an automation system for a gas boiler house, it is planned to install control panels based on the Kontar MS 8.3 controller. For the device of the dispatching system - a control unit based on the controller "TWDLCAE40DRF". The transmission of the following information is provided: signals of emergency situations in the technological part of the boiler room, signals of gas contamination, security and fire alarms of the boiler room, parameters of the boiler room. For the security alarm device, the installation of the S2000-4 control panel, the Touch Memory reader and the Pyronix Colt XS and IO 102-20 security detectors is provided. To control the mass concentration of carbon monoxide (CO) and the volume concentration of methane (CH4) in the boiler room, an ESSA-CO-CH4 gas analyzer is installed. For commercial metering of gas consumption, the installation of a gas corrector LNG 761.2 (manufactured by AOZT NPF Logika) is provided. The transmission of data on gas consumption is provided through the GSM-modem "RU-MC55iT" to the control room. For security and fire alarm systems, installation of equipment of the integrated security system of the NVP Bolid company is provided. As the control equipment, it is planned to install: the S2000M control and control panel, the S2000-KPB control and launch control unit, with boron for receiving and control and control of automatic fire extinguishing means PPKU ASPT "S2000-ASPT". The heating of the boiler room is designed to maintain a temperature not lower than +5°C and is solved due to heat transfer from process equipment and pipelines and the use of electric thermal curtains (switched on by a temperature sensor). In the premises of the boiler room and the diesel generator room, supply and exhaust ventilation with natural induction is provided, designed for three times the air exchange of general ventilation, as well as providing the air flow necessary for fuel combustion and removal of excess heat from the diesel generator. Air inflow for general and technological ventilation is designed through louvered grilles in external enclosures, air removal - through deflectors on the roof of the building. To remove excess heat from the diesel generator, a grate is provided in the outer enclosures. Measures for noise suppression and fire protection are provided.