Did not you find what you were looking for? Ask us! We have archives of 140 TB. We have all modern reuse projects and renovation projects for Soviet standard buildings. Write to us: info@proekt.sx
Boiler house project 6 MW
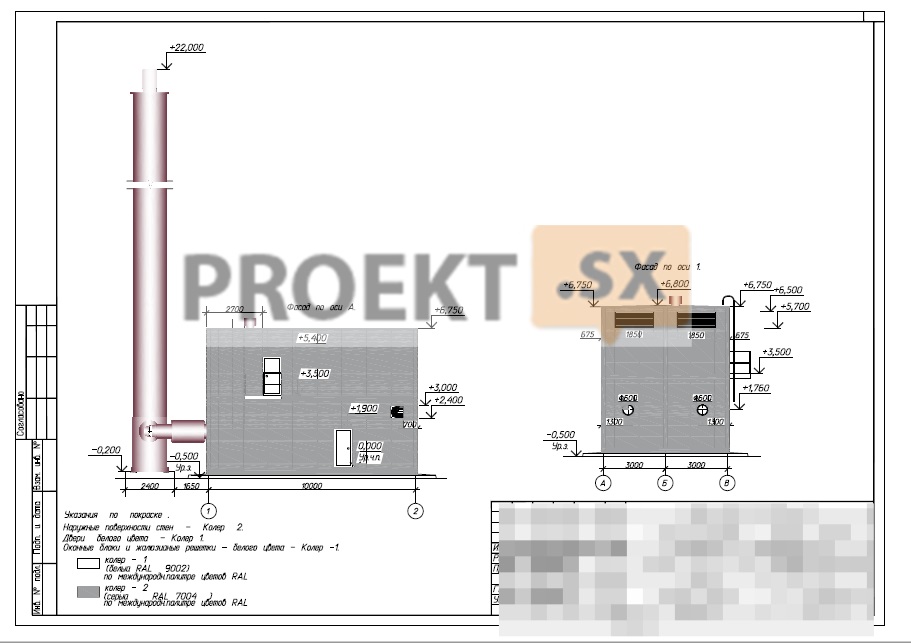
Design, working documentation, including estimates, and the results of engineering surveys for the construction of an automated gas
boiler house and heating networks
Technical and economic characteristics of the capital construction object
Plot area, ha: 0,0330
Building area, m2: 75,5
Total building area, m2: 120,0
Construction volume of the building, m³: 442,3
Length of heating networks, running meters: 345
Number of floors, fl.: 2
Productivity, MW: 6
Estimated cost at the 2001 base price level (without VAT)
Total: thousand rubles: 14884,75
Construction and installation works, thousand rubles: 3364,66
Equipment, thousand rubles: 10020,02
Other expenses, thousand rubles: 1500,07
including :
PIR, thousand rubles: 930,51
refundable amounts, thousand rubles: 14,96
Estimated cost at current price level October 2010 (including VAT)
Total: thousand rubles: 58637,25
Construction and installation works, thousand rubles: 17119,24
Equipment, thousand rubles: 34288,50
Other expenses, thousand rubles: 7229,51
including:
PIR, thousand rubles: 3350,42
VAT, thousand rubles: 8944,67
refundable amounts, thousand rubles: 76,12
Structural and space-planning solutions
The modular boiler house is designed from easily assembled metal structures with sandwich panel cladding (2-storey structure of 4 interlocked block modules). Metal structures are designed from a closed bent profile 80x4, etc. (connections from a bent profile 60x5) according to GOST 8639-82. Beams - from I-beams 20B1 according to STO ASChM 20-93. External walls - hinged sandwich panels 100 mm thick. Covering - from a sandwich panels 100 mm thick on a metal frame. Spatial rigidity and stability is provided by vertical and horizontal connections. The foundations are taken in the form of a monolithic reinforced concrete slab 200 mm thick, concrete B15, W6, F75. A 100 mm thick concrete preparation is provided under the foundation. Chimneys in the constructive section were not considered. Foundations for pipes - columnar concrete B25, W6, F75, designed for loads specified by the customer. The relative mark of 0,000 corresponds to the absolute mark of 18.25. In accordance with the report on engineering and geological surveys, the base of the foundations are light silty ferruginous semi-solid loams with E=120 kg/cm2, φ=22°. The design resistance of the foundation soils is not lower than R=1,63 kg/cm2. The pressure on the ground does not exceed p=0,42 kg/cm2. In order to protect the concrete of underground structures, the concrete grade for water resistance is W6 on sulfate-resistant concrete, the concrete surface is protected by coating with bitumen twice. The expected average settlement of the building is no more than 0,6 cm. The stability of the pipes is ensured.
Engineering equipment, utility networks, engineering activities
For heat supply of heat consumption systems of the quarter, a block-modular automated gas stand-alone boiler house was designed. According to the explosion and fire hazard and the degree of fire resistance, the boiler room belongs to the category "G" and "II". The installed capacity of the boiler house is 6000 kW. As easy-to-reset structures at the rate of 0,03 m2 per 1 m3 of the volume of the boiler room, a part of the easy-to-reset roof with an area of 63,24 m2 is provided. Heat consumers belong to the second category in terms of heat supply reliability. The boiler house is equipped with two water-heating boilers of the TT100 type with a heat output of 3000 kW each, with Oilon gas burners. Estimated heat load at DHW avg, taking into account losses in the networks and auxiliary needs of the boiler house - 4527,5 kW, including: for heating - 3554,2 kW; for hot water supply, average - 779,2 kW; for losses in heat networks - 170,8 kW; own needs of the boiler house - 23,3 kW. The main type of fuel is natural gas QpН=33520 kJ/m3 (8000 kcal/m3). The operating mode of the boiler house is year-round. The scheme for connecting heat networks intended for transporting heat carriers to heating and hot water systems is independent. It is planned to control the temperature of the coolant depending on the outside air temperature. Regulation of the boilers and maintaining the necessary parameters of the coolant is provided by the automation of the boiler room. The operation of the boiler room is in automatic mode, without the constant presence of service personnel. The water temperature at the outlet of the boilers is 110°C. The heat carrier at the outlet of the boiler room is water with a temperature of - 95°C (for heating systems), and with a temperature of 65°C (for hot water systems). To maintain the water temperature in front of the boiler (70°C), a three-way valve is installed. To compensate for the thermal expansion of water in the heat supply system, expansion tanks are installed for each boiler unit V = 600 l. Auxiliary equipment is installed in the boiler room: boiler circuit pumps IL150/200-7,5/4 and IP-E80/115-2,2/2; network pumps of the heating circuit - BL 80/150-15/2; network pumps of the DHW circuit - МНI802; heat exchangers lamellar heating systems M15-MFM; plate heat exchangers for hot water supply M6FG; water softening unit TEKNA APG 603. To account for the consumption of thermal energy, it is planned to install a metering unit based on the PREM 150 flow meter. To remove combustion products, metal individual gas ducts and chimneys 22 m high and 550 mm in diameter were designed. Thermal insulation of heat pipelines, gas ducts and equipment is provided. For gas supply to the equipment of the boiler room, according to the Specifications, it is planned to lay a medium-pressure steel gas pipeline with a diameter of 80 mm from an above-ground steel medium-pressure gas pipeline laid along the facade of the boiler room and linked to the project documentation. The gas pressure at the inlet to the boiler room is 0,2 MPa. For commercial accounting of the amount of gas, a gas meter STG-80-250 is installed. The maximum gas consumption is 700,96 m3/h. At the entrance of the gas pipeline to the boiler room, the following are installed in series: thermal shut-off valve KTZ 001-80, solenoid valve VN3N; gas filter FN3-1. Reserve fuel supply is not provided. Design solutions provide for the possibility of operating a boiler house on liquid fuel. The heat load of heat consumption systems at DHWmax is 5666 kW. The heat carrier is water with Т1/Т2 = 95/70°С, Т3=65°С. Design pressure at the connection point: Р1-Р2=1,5 kgf/cm2, Р2=2,7 kgf/cm2, Р3=3,77 kgf/cm2. The connection point is the collector of the boiler room. The heat supply scheme is four-pipe. Laying of the heating network - underground and aboveground on the technical underground of buildings. For laying a heating network, it is planned to use steel electric-welded pipes in accordance with GOST 10704-91 in PPU insulation with a remote control system device (ODK), for laying hot water pipelines - polypropylene PPR pipelines. Compensation for thermal elongations is solved due to the angles of rotation. The connection scheme for heating systems and hot water supply systems is dependent. To receive thermal energy, adjust the parameters of the coolant and supply heat to consumers, it is provided for the device in each building of individual heating points with automation devices, a set of shut-off and control and safety valves, heat energy metering units. Water supply (cold water) and water disposal of the consumers of the facility is provided in accordance with the technical conditions for connection to the public water supply and sewerage system. Water supply (cold water) is provided from water supply networks D=225 mm through two inlets made of polyethylene pipes according to GOST 18599-01 D=110 mm. At the inputs, the device of water measuring units is provided. Guaranteed pressure at the connection point - 25,0 m w.c. Estimated consumption of cold water - 143,69 m³ / day. The required pressure for the integrated water supply system is 22,0 m of water. PVC water pipes were chosen for the construction of the drinking water supply system. External fire extinguishing is provided from fire hydrants D=125 mm installed on water supply networks. Water consumption for external fire extinguishing - 10,0 l / s. Discharge of domestic wastewater in the amount of 12,30 m³/day and periodic discharge - 11,47 m³/day (1 time per year) are provided for in the nearest manhole on the street sewerage network. The drainage of rainwater with a flow rate of 0,79 l / s is provided through external drains to the relief and further to the storm water well on the street network of combined sewerage. Household sewage systems (for the removal of conditionally clean effluents from boiler equipment) and external drains were designed for the building. Cast-iron sewer pipes were chosen for the device of the domestic sewerage system. In accordance with the technical specifications for the technological connection of the electrical installations of the boiler house to the electrical networks, two independent mutually redundant power sources of the boiler house are the 1st and 2nd sections of 10 kV PS220/10 kV. The connection point is installed in the ASU-0,4 kV boiler room. The power supply of the boiler house is provided by two mutually redundant CL-0,4 kV. The design documentation provides for the installation of a certified, mass-produced block boiler house of complete factory readiness "Signal 6000". The main consumers of electric energy of the boiler house are: network pumps, recirculation pumps of the boiler circuit, burner fans and fuel pumps of boiler units, cold water booster pumps, control system. With regard to the reliability of power supply, the complex of electrical receivers of the boiler house belongs to the second category; fire, security alarm, gas analyzer, control and dispatching system of the boiler room - to the first category. Restoration of power in the event of a power failure of the boiler room from one of the sources: for power receivers of the 1st and 2nd category, automatic, by the action of the ATS AVR-0,4 kV boiler room. The power supply scheme adopted in the design documentation satisfies the requirements for the reliability of power supply to consumers of the designed facility. The estimated electrical load of the boiler room is 61,6 kVA. The security system was adopted by TN-CS with a device at the input to the boiler room for re-grounding the neutral conductor and the main potential equalization system. The PE VRU-0,4 kV bus is used as the GZSH. As a grounding conductor, natural grounding conductors (reinforced concrete foundations of the chimneys of the boiler house) and an artificial grounding conductor combined into one device are used. The steel lightning rod is installed on the chimneys and connected to the earth electrode through the steel frame of the chimneys. In accordance with the contract for the provision of communication services, the boiler room is connected to the existing city telephone network. The connection point is set at the inlet cross-section of the boiler house. Through communication networks, the boiler room is connected to a single dispatching system. The main communication channel is wired, the backup is a radio channel (GSM / GPRS modem); the system automatically selects a communication channel with priority on the wired Internet. Emergency and technological (including accounting and information) signals are automatically transmitted to the control room. Upon receipt of an emergency signal, the dispatcher by phone sends the duty group closest to the boiler house that gave the signal. The control room and duty groups operate around the clock. The list of signals transmitted to the dispatching system: emergency: 1st and 2nd methane gas levels, 1st and 2nd carbon monoxide levels, malfunction of the gas analyzer, fire in the boiler room, unauthorized entry into the boiler room, minimum cold water pressure, minimum gas pressure at the inlet to the boiler room, shut-off gas valve closed, failure of boiler circuit pumps, lack of power from the external network, failure of all pumps; technological: temperature and pressure in the direct and return pipelines of the heating network, temperature and pressure in the boiler circuit, temperature and pressure of hot water in the direct and return pipelines; accounting: gas consumption, cold water consumption, heat generation in the heating circuit; information signals: a signal of non-normative replenishment of the heating circuit, authorized and unauthorized entry into the boiler room.